As we all know, the operation of rotary kilns is part of the process of producing Portland cement and lime. These rotary kilns are usually large horizontal cylinders with a slightly higher feeding end that uses gravity to push the product through the kiln, slowly rotating the material inside and working continuously at very high temperatures. The rotary kiln is lined with dense firebrick to protect the steel shell from high heat in the kiln. The firebrick lining of the rotary kiln must have a high enough density in order to withstand long periods of harsh mechanical wear when the material is constantly rolling through the kiln. This high density refractory, while effectively resisting wear, also has some negative effects. First, dense refractories have high thermal conductivity and wear over time, leading to an increase in the temperature of the casing. As fuel prices continue to rise, the problem of high energy consumption has greatly affected costs. The increase in the temperature of the kiln shell also has a negative impact on the safety of mechanical drives and personnel working in the area. Moreover, high density refractory materials will flake or crack seriously when the temperature changes dramatically or the temperature gradient between hot and cold surfaces of bricks is large.
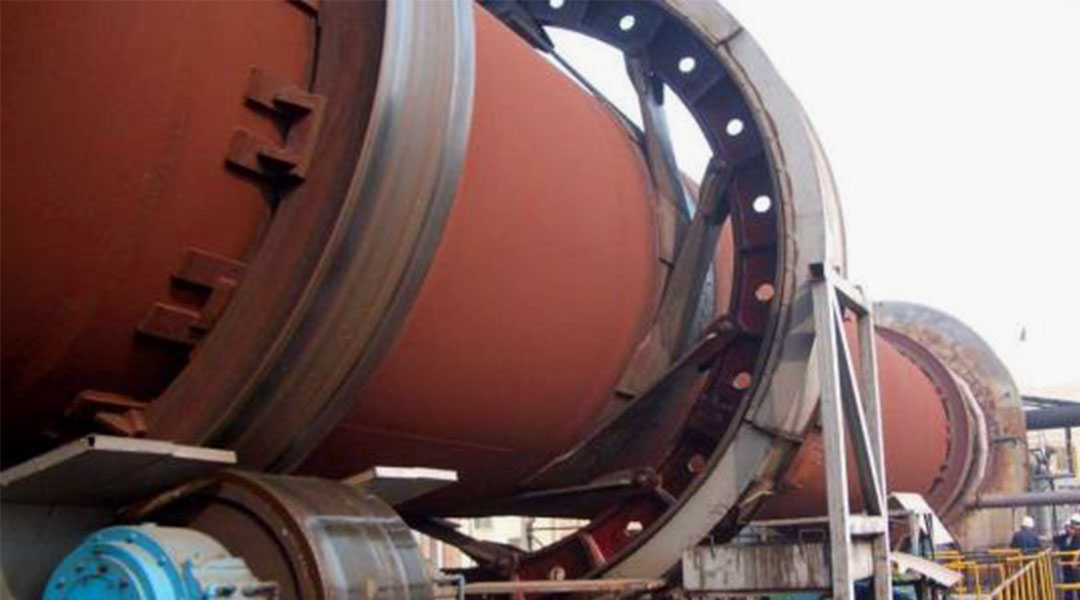
Therefore, the following points must be considered in the selection of appropriate thermal insulation materials:
---Heat resistance of thermal insulation material
---Thermal conductivity of thermal insulation layer
---Mechanical properties of thermal insulation material
---Insulation layer thickness, the thinner the better
Aiming at the performance requirements of rotary kiln, the team of Zerothermo found through testing that the company's high temperature nano Microporous insulation panel is a very suitable material for reducing the temperature of the kiln shell, reducing heat loss, extending the life of the equipment and increasing the output. Rotary kiln adopts the advantages of high temperature nano heat shield panels:
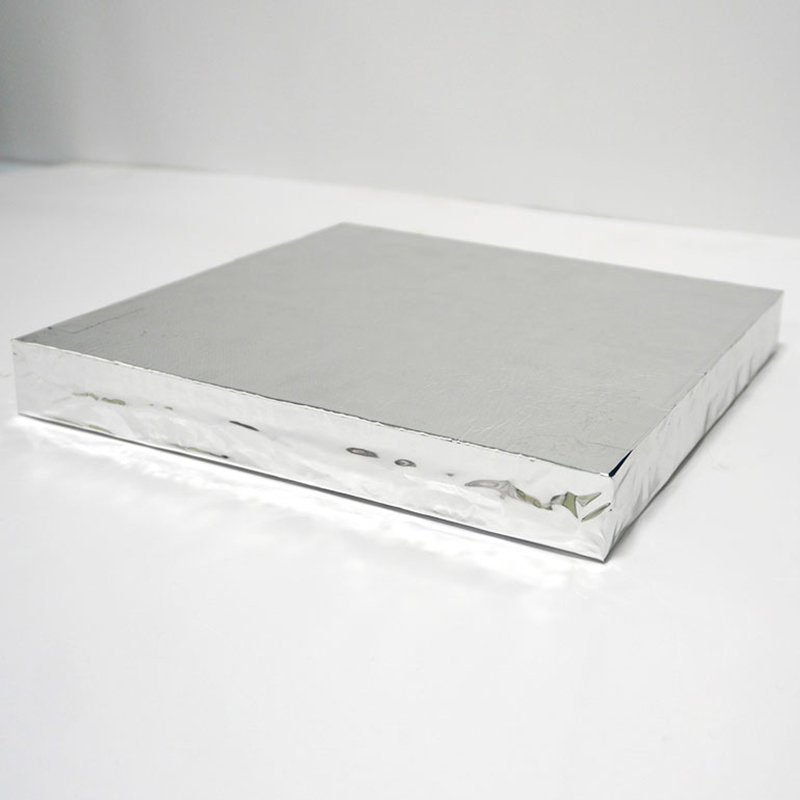
Because microporous insulation minimizes the effect of heat from all three modes (conduction, convection, and radiation), it has the lowest thermal conductivity of all high temperature resistant adiabatic materials. This will greatly reduce heat loss through the lining and reduce energy consumption.
Placing thermal insulation material behind the insulated firebrick will reduce the thermal gradient of the firebrick, and the refractory is not easy to have thermal shock, so it can extend the life of the furnace lining.
Reduce the temperature of the kiln shell and the heat absorbed by the drive device by reducing the heat loss of the lining.
It is very easy to install, only need to use air curing refractory mortar or contact adhesive should be fixed in the interior of the kiln.
The microporous plate is thin, the standard thickness is 3mm to 15mm, which can save cost and space
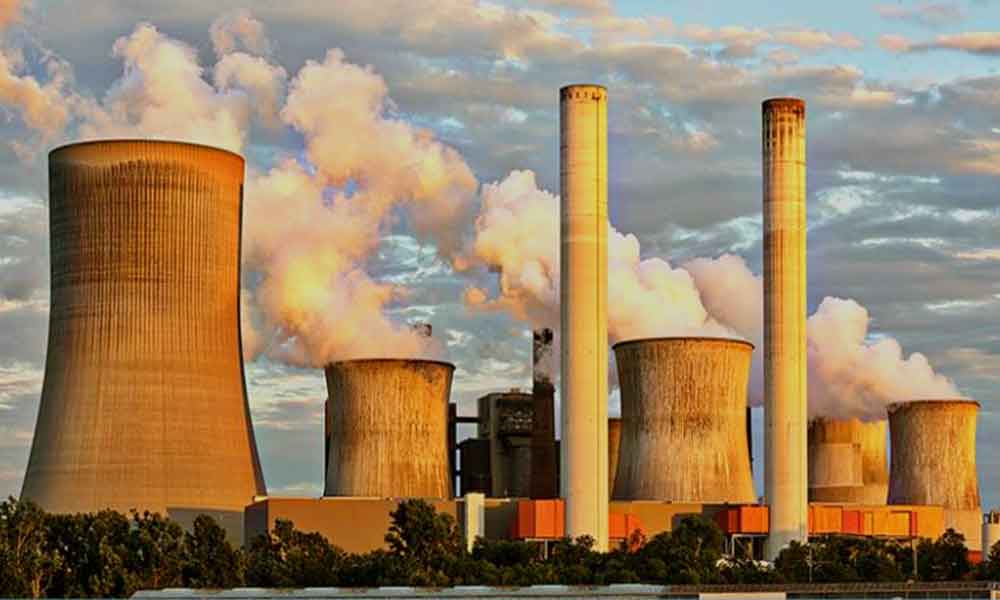
To sum up, the use of nano-mircoporous insulation panel with refractory materials and cylinders can greatly reduce heat loss, provide kiln and mechanical drive life, improve kiln load and protect the safety of the operator. This kind of materials reduce energy consumption and operation cost increased energy conservation and emission reduction requirements are of great significance.
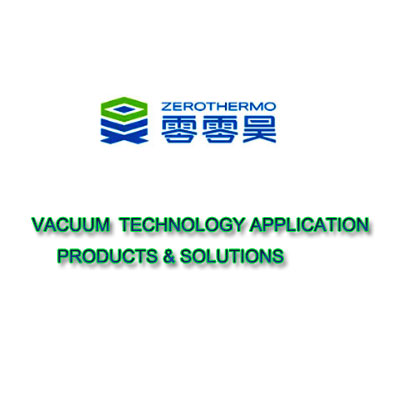
Zerothermo focus on vacuum technology for more than 20 years, our main products : vacuum insulation panels based on fumed silica core material for vaccine, medical, cold chain logistics, freezer, integrated vacuum insulation and decoration panel, vacuum glass, vacuum insulated doors and windows. If you want to learn more information about Zerothermo vacuum insulation panels, please feel free to contact us, also you are welcome to visit to our factory.
Sale Manager: Mike Xu
Phone :+86 13378245612/13880795380
E-mail:mike@zerothermo.com
Website:https://www.zerothermovip.com
Post time: Feb-14-2023